Having an old press brake machine is like a headache for owners. You go into the dilemma of whether to keep it or sell it. However, replacing the old machine can be a costly deal and logistics can be an added challenge.
But how about retrofitting your existing press brake with parts like LVD press brake or Mazak used parts with increased efficiency? This will help reduce setup time, scrap and even your operator or you will not be skeptical about learning a new press brake machine.
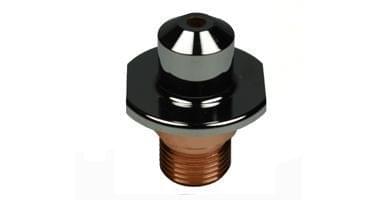
1. Evaluate the Machine’s Condition:
Before performing anything to your machines, you need to study the current condition and know the ins and outs of it.
Make sure you are considering the following things before making any changes.
- Accuracy:
Check the current bending accuracy of your sheets. This depends on the bending method you are using. Are you using coining, bottom bending or air bending for sheet metal?
While checking the accuracy, if you find out that your sheet is bending accurately maintaining all the standards, then there is no need to replace your machines.
In such scenarios, some changes here and there will make all the difference.
- Pedestal Control:
Having proper pedestal control is important. For many Original Equipment Manufacturers (OEMs), having proper pedestal control is important because without these having programmable logic boards are difficult.
Researching the availability of these components can be a perfect solution rather than investing in a new pedestal control.
- Press Brake Control:
Having control over the press brake machine is important. There are various ways to control the press brake. You can either control it manually or with a programmable control head.
In such scenarios, it is important to understand that retrofitting your machine can be difficult and may turn out to be an expensive solution.
But, if the machine is running properly without the need for any digital control then a basic change in it will work for you.
2. Know your machine:
There are various types of press brake machines, parts like LVD press brake, Mazak used parts available in the market. Each of them has different functionalities and features. In such scenarios, you need to understand your machine thoroughly.
3. Understand the pain points:
As the press brake owner or the operator, you need to understand the obstacles you come across while using it. For example, if you frequently move the tool, then you will need to keep adjusting the height of your gauging surface.
In such cases, you need to understand what can be a better option when it comes to working with its tools.
- Depth/ Angles:
Are you manually adjusting the ram depth or angle often? If so, you can increase the productivity by adding the ram axis or Y axis to the back gauge or front gauge.
4. Proper Approach:
If you opt for retrofitting your press brake machine, then, then there are companies doing the same work. They may ask you the overall length of the press brake machine, the distance between the side frame, usage, type of sheet metal are you bending, etc.
They would also ask if is it a single or multiple operated supporting sheets, the control capabilities, and many such things.
Many companies have different controls for different applications. You can use them for things like go-to-positions-style control, make one-off parts or PC based control like networking, offline programming or unlimited storage.
It says that sophisticated control offers great benefits, but in reality, they require more front-end planning. Because these companies require accurate measurements of your tooling.
Wrapping it up:
Having a press brake and maintaining should not be a headache. Before taking any major steps, it is better to rethink, reuse for increased efficiency.